Crafted from high-quality materials, domed end caps are integral components in numerous industrial and domestic applications. These versatile products serve as the end closure for cylindrical objects like pipes and tanks, ensuring reliability and safety across various sectors. To further the understanding of these essential items, it’s crucial to delve into their diverse applications, manufacturing processes, and the advantages they offer.
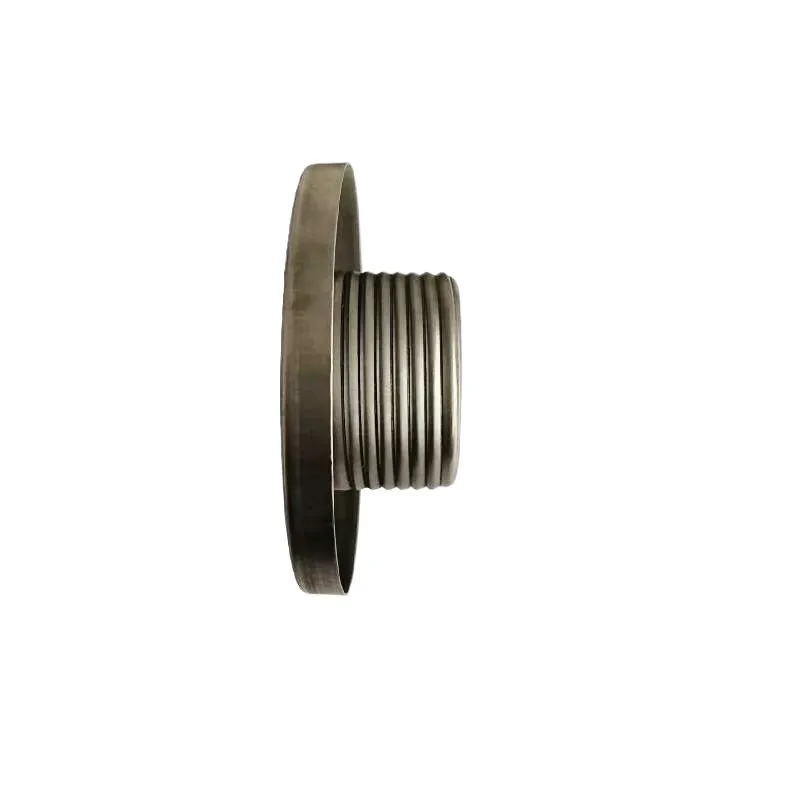
Domed end caps come into play predominantly in the realms of pressure vessel manufacturing, oil and gas industries, and the construction of boilers and tanks. They are designed to withstand immense pressure, which prevents leaks and maintains the structural integrity of the vessel. The specialized shape, with its outward curve, maximizes the strength of the end cap by distributing the stress evenly across its surface. This is in contrast to flat end caps, where stress concentration can lead to material fatigue and eventual failure.
Manufacturers employ various techniques to produce domed end caps, each chosen based on the specific requirements of the job. Methods such as spinning, deep drawing, or hot forming are often used. The material factors heavily into the choice of technique; stainless steel, carbon steel, and aluminum are popular choices due to their durability and malleability. Spinning, for instance, involves the rotation of a metal disk while pressure is applied to mold it into the desired dome shape. Deep drawing,
on the other hand, involves pulling the metal into shape using a die. Each method requires precision, with manufacturers employing advanced technology to ensure every end cap meets stringent industry standards.
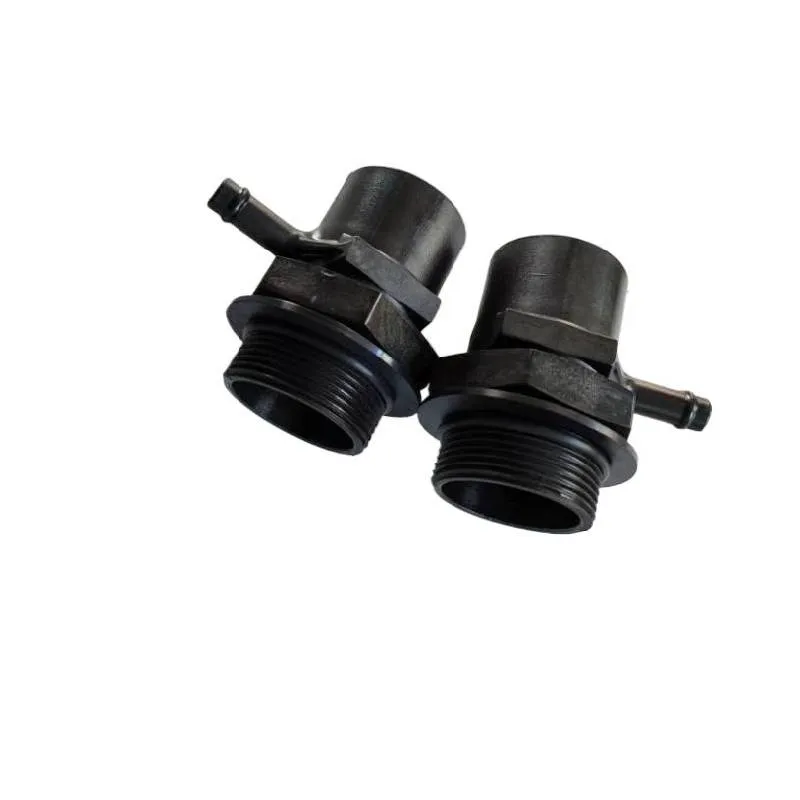
The expertise of a manufacturer is particularly crucial when choosing the right domed end cap for your needs. A skilled manufacturer will understand the specific requirements of your application, providing guidance on the appropriate materials, dimensions, and thickness needed. Companies with a long-standing reputation in the industry often offer bespoke services, which can be invaluable for complex projects requiring custom specifications. Expertise in thermodynamics and material science further ensures that these manufacturers can support the development of high-pressure systems that operate safely under extreme conditions.
domed end cap
The environmental impact of manufacturing is a growing concern in today's eco-conscious landscape, and the production of domed end caps is no exception. Forward-thinking manufacturers are actively working to reduce their carbon footprint, opting for sustainable practices throughout the production process. This includes recycling of materials, efficient energy use, and reduction of waste, aligning with global efforts to create more sustainable industrial practices. In choosing a manufacturer committed to environmental responsibility, companies not only comply with regulations but also enhance their reputation as stewards of sustainable progress.
When it comes to installation and maintenance, the trustworthiness of the domed end cap is paramount. Given their critical role in maintaining system integrity, any failure can lead to significant downtime, safety hazards, and costly repairs. Thus, sourcing domed end caps from established suppliers with proven track records is advisable. These suppliers should offer comprehensive warranties and after-sales support, ensuring any issues are promptly and effectively addressed. Regular maintenance checks and professional installations further bolster the dependability of these components, safeguarding them from premature wear and tear.
Safety standards and certifications are crucial to consider when selecting a domed end cap. It’s essential that the product complies with industry-specific regulations such as the ASME Boiler and Pressure Vessel Code in the United States, which ensures the end caps meet necessary safety and performance benchmarks. In selecting certified products, companies not only comply with regulations but also contribute to overall safety and workers' well-being.
In conclusion, domed end caps are a testament to engineering ingenuity, providing critical support across myriad industries. By understanding their applications, manufacturing processes, and the importance of selecting a reputable supplier, businesses can optimize their operations while ensuring safety and compliance. As industries evolve, the demand for high-quality, sustainable, and reliable domed end caps will undoubtedly continue to grow, solidifying their indispensable role in industrial applications worldwide.