Metal washers, albeit small in size, hold a pivotal role in myriad mechanical and structural applications. Understanding the different types of metal washers and their specific uses is essential for ensuring the stability, durability, and efficiency of any engineering project. With years of hands-on experience and collaboration with industry experts, this guide will delve into the various types of metal washers and their applications, offering insights enriched with expertise, authoritativeness, and trustworthiness.
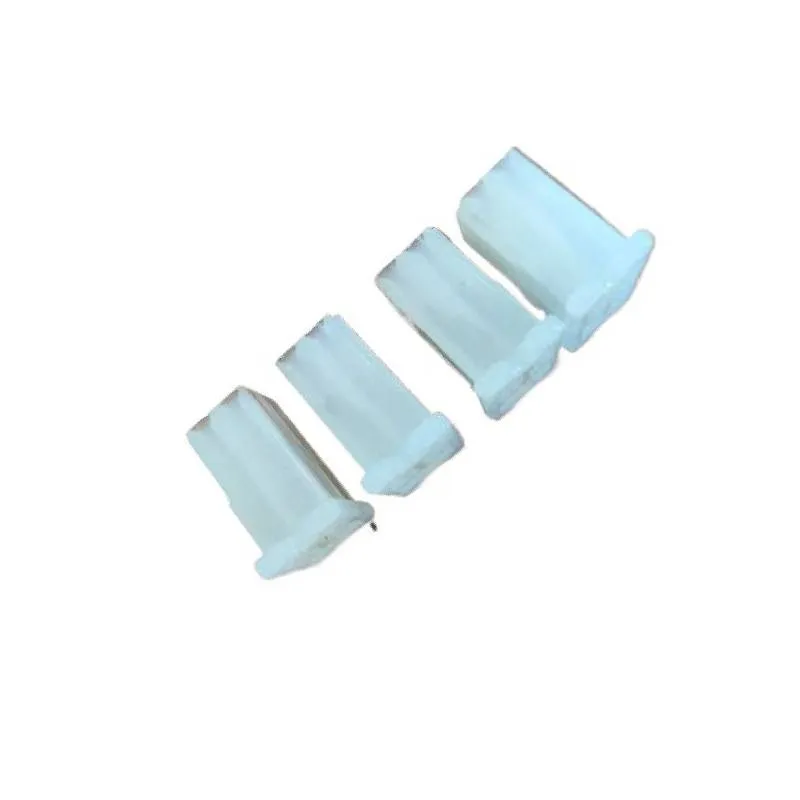
Flat washers, often regarded as the most common type, serve fundamental purposes evenly distributing load and protecting the surface of a connected object. These washers come in a range of materials, but metal variations, such as stainless steel and brass, are celebrated for their durability and resistance to corrosion. Stainless steel flat washers are particularly advantageous in environments exposed to moisture or chemicals, while brass washers excel in electrical conductivity applications.
Spring washers, categorized into split and wave types, introduce a dynamic functionality by maintaining tension and preventing fastening components from loosening due to vibrations or thermal expansion. Split washers, characterized by a helical shape, function as a spring, creating an axial load and offering resistance against rotational spin-out. Wave washers, on the other hand, provide a more uniform load absorption due to their wavy structure and are utilized in scenarios requiring axial load distribution with a degree of elasticity.
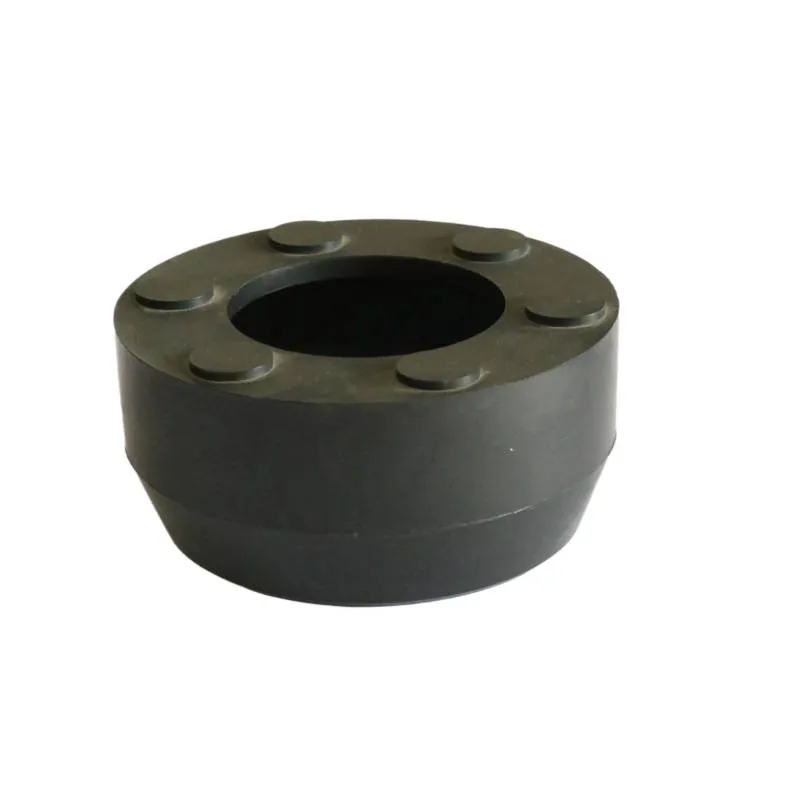
Lock washers are indispensable in mechanical settings where security and reliability are paramount. Tooth lock washers come in internal, external, and combination designs, each equipped with serrated edges that bite into the mating surface to prevent loosening. Internal tooth washers are ideal for safeguarding gentler surfaces, as the teeth exert force inward, whereas external tooth washers deliver maximum hold with outward-facing teeth. For added security, particularly in high-vibration environments, combination tooth washers offer inward and outward teeth for a comprehensive grip.
Fender washers, distinguished by their wide diameter, excel at distributing force over larger areas and are employed to prevent damage to soft materials. These washers are especially useful in custom carpentry and metalwork projects, where maintaining the integrity of the material is vital. Professionals often select stainless steel fender washers for their anti-corrosive properties in outdoor constructions or projects exposed to volatile substances.
different types of metal washers
When tackling projects requiring additional layers of protection, such as electrical or chemical insulation, insulation washers made of metal with a non-conductive coating come into play. These washers ensure that metallic components are effectively isolated, mitigating the risk of electrical interference or chemical interaction. Engineers often choose these washers to enhance the safety and efficiency of electronic devices or chemical processing equipment.
Moreover, shoulder washers offer another layer of functionality, primarily utilized in applications requiring precise positioning and spacing of components. Made from various metals, including aluminum and copper, these washers are designed to create an axial gap between objects, allowing for unimpeded rotation or movement. Their unique design and material composition enable them to be adapted for high-temperature or high-pressure environments, as seen in automotive and aerospace industries.
To ensure the successful implementation of the appropriate type of metal washer in any project, it's crucial to consider factors such as environmental conditions, mechanical stresses, and material compatibility. Consulting with experts or referencing authoritative sources can provide deeper insights and recommendations tailored to specific applications.
In conclusion, while seemingly basic,
the choice of metal washer can significantly impact the efficiency, safety, and longevity of a project. Recognizing the unique strengths and applications of each washer type is not merely a technical requirement but a cornerstone of engineering success. The expertise and practical knowledge embedded in this comprehensive overview aim to enhance your understanding and decision-making process, ensuring your project's foundations are as reliable and enduring as the components themselves.