Custom plastic parts are revolutionizing industries ranging from automotive to aerospace, transforming how products are designed, manufactured, and utilized. These components are not merely replacements for traditional materials but bring unparalleled benefits that cater to specific industry demands. This article dives into the unique advantages of custom plastic parts and why they should be considered by manufacturers seeking innovation and efficiency.
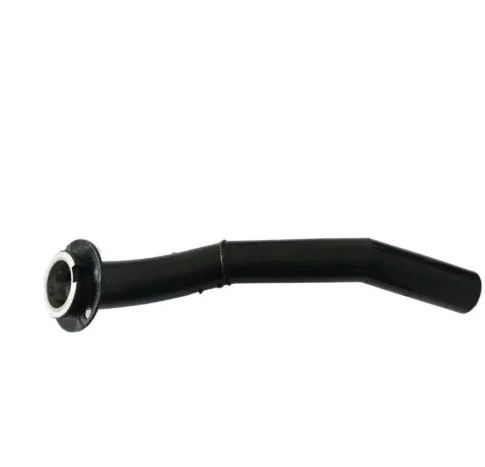
In the ever-evolving landscape of product manufacturing, precision and adaptability are key.
Custom plastic parts offer flexibility that is unrivaled, providing tailored solutions for complex engineering challenges. This flexibility is achieved through advanced techniques such as injection molding, 3D printing, and CNC machining, each offering specific benefits depending on the project requirements. With injection molding, for instance, manufacturers can produce high volumes of parts with remarkable consistency and at a lower cost per unit once the initial tooling investment is made.
For industries with more specific needs, 3D printing presents a groundbreaking alternative. Its capacity for rapid prototyping and low-volume production allows for extensive testing and development at a reduced cost. This method grants designers and engineers the freedom to create intricate geometries that were once impossible with traditional methods. As a result, industries can optimize their designs for performance, reduce waste, and decrease time-to-market, thus aligning with sustainable practices and cost-efficiency.
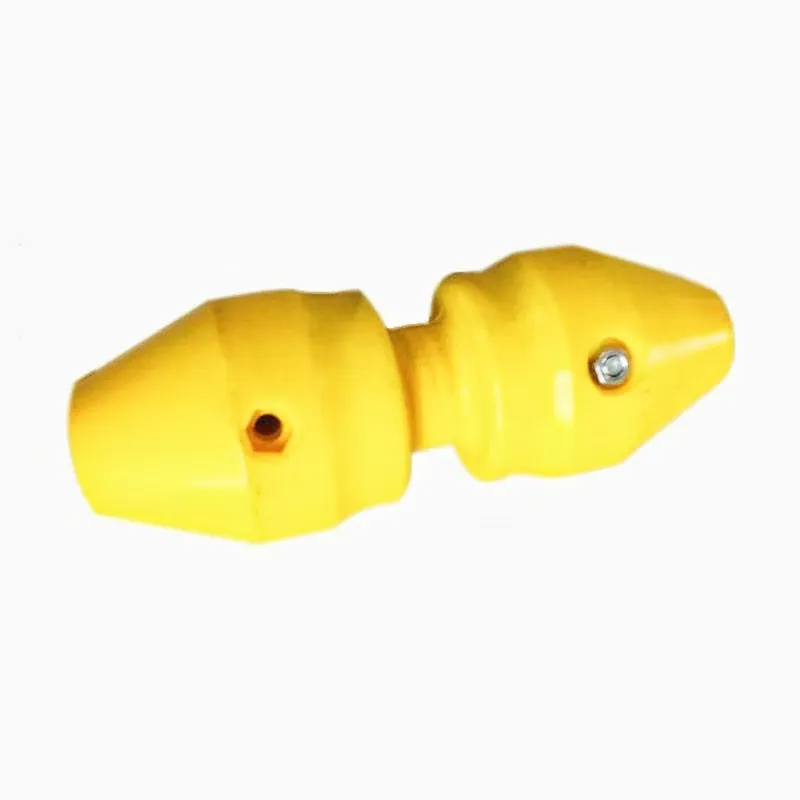
When discussing the professionalism inherent in custom plastic parts, one cannot overlook the expertise required in customizing these components. Knowledge in material science is critical, as different polymers offer varied properties necessary for strength, flexibility, resilience, and heat resistance. For instance, choosing the right polymer can influence a part's performance under thermal stress or its ability to withstand chemical exposure. The material selection process is integral, demanding a deep understanding of both the application's requirements and the materials' capabilities.
custom plastic parts
Moreover, engaging with a reputable manufacturer brings a layer of authoritativeness and trustworthiness to your project. A company with a well-established track record not only ensures high-quality production processes but also offers insights backed by years of experience in the field. Trusted providers often have certifications and adhere to stringent quality control measures, ensuring the parts produced meet international standards and perform as expected in real-world applications.
Reliability in supply chain and production is another area where custom plastic parts shine. By collaborating closely with suppliers, manufacturers can achieve a responsive and adaptable production line. This collaboration minimizes supply chain disruptions and allows for just-in-time manufacturing, which reduces inventory costs and enhances efficiency.
The application of custom plastic parts extends beyond simple usage; it is about creating smarter, more efficient systems. For example, in the automotive industry, custom plastic components contribute to lightweighting vehicles, thus improving fuel efficiency and reducing emissions. In the medical field, biocompatible plastics are paving the way for safer medical devices and implants, showcasing the critical role these materials play in enhancing product functionality and safety.
In conclusion, the value of custom plastic parts lies in their ability to transform ideas into tangible solutions that drive innovation across various sectors. By leveraging the expertise of seasoned professionals in the field and utilizing advanced manufacturing techniques, businesses can achieve greater adaptability and efficiency. It is clear that investing in custom plastic components not only enhances product performance but also bolsters a company’s commitment to quality and sustainability, which are key tenets in today’s competitive market.