For anyone engaged in the world of industrial applications, choosing the right sealing solutions is a critical decision. Among the various options available today, the bonded seal ring stands out for its unique blend of performance, reliability, and versatility. Known for bridging the gap between elastomeric seals and rigid metal ring-based designs, it has become a go-to choice for industries that demand both strength and flexibility.
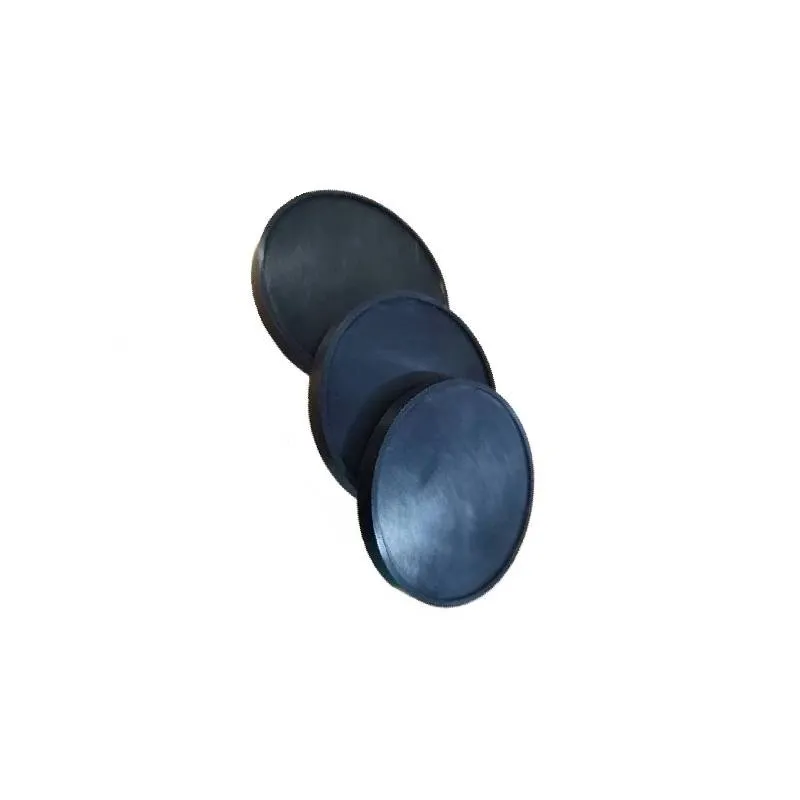
The bonded seal ring is a composite gasket comprising an elastomer layer bonded to a metal ring. This combination ensures that the seal retains the flexibility to accommodate surface irregularities while providing the robustness of metal, making it an ideal choice for static and dynamic applications alike. Originally developed as a solution to address the leakage issues in hydraulic systems, its applications have now expanded across a multitude of industries, including automotive, aerospace, and marine sectors.
One of the significant advantages of the bonded seal ring is its suitability for high-pressure applications. The metal ring provides a strong support structure, preventing extrusion and ensuring longevity under demanding conditions. This makes it particularly beneficial in hydraulic systems where consistent performance is non-negotiable. Additionally, the elastomer element can be tailored according to specific media compatibility and temperature range requirements, further enhancing its adaptability.
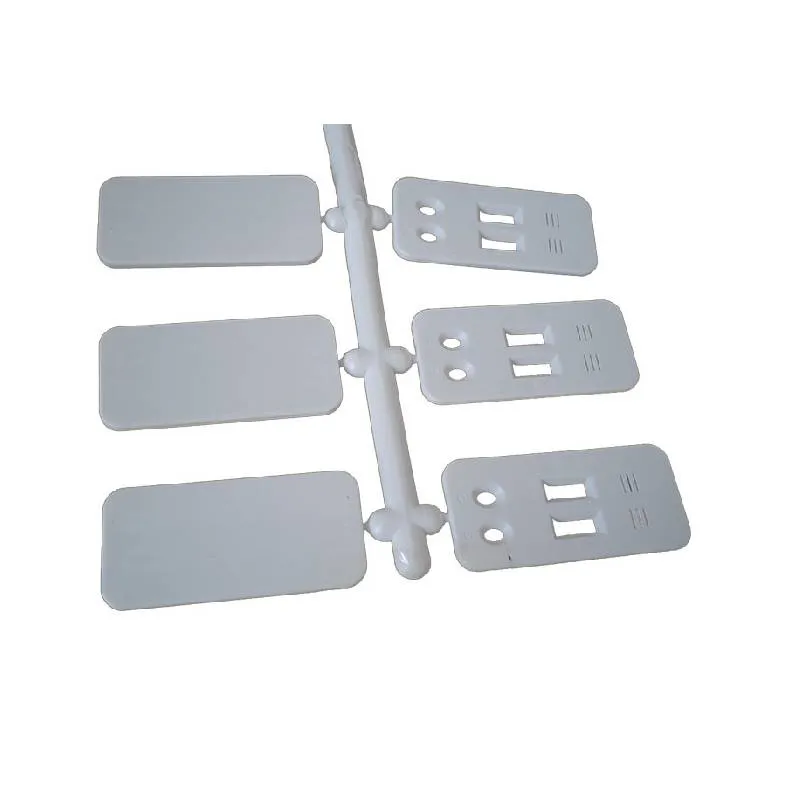
From a professional standpoint, the ease of installation and maintenance of bonded seal rings cannot be overstated. Unlike traditional gaskets which often require precise fitting and delicate handling, these seals are user-friendly, reducing machine downtime and increasing operational efficiency. Their pre-formed design ensures consistent sealing performance right out of the box, contributing to reduced wear and tear on machine components.
bonded seal ring
Experts in the field highlight the importance of selecting the correct material compositions when considering bonded seal rings. Given the diverse applications, manufacturers provide options in both the rubber component and metal, commonly using materials like nitrile, fluoroelastomer, or silicone, paired with metal options such as stainless steel or carbon steel. This flexibility allows users to select a seal that best fits the chemical compatibility, pressure, and temperature requirements of their specific application.
Authority in this domain comes from understanding these nuances and leveraging them to optimize machinery and improve reliability. Engineers and maintenance experts recommend integrating bonded seal rings as part of an overall strategy to enhance machine performance and decrease unscheduled downtimes. Trust is built when a product repeatedly performs as expected, and this trust is well-placed in bonded seal rings owing to their robust design and proven performance track record.
For anyone evaluating sealing solutions, the bonded seal ring offers a compelling blend of versatility, durability, and ease of use. It exemplifies a product whose design evolution keeps pace with the needs of demanding industrial environments, offering professionals a reliable option with a history of effective performance. As industries push the boundaries of what machinery can do, selecting the right components—like the bonded seal ring—is critical in paving the way for innovation and progress.