A bellows mechanical seal stands out as a pivotal component in industrial applications, renowned for its efficacy in mitigating fluid leakage. This indispensable device marries functionality with durability, providing unparalleled solutions across various sectors, from chemical processing to oil and gas industries.
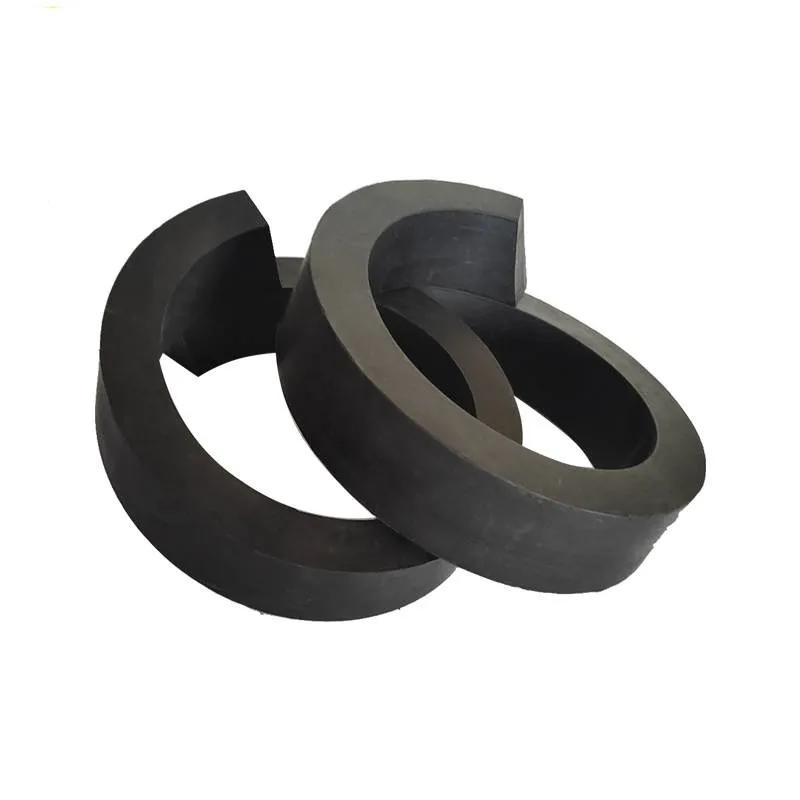
In essence, a bellows mechanical seal is engineered to address the limitations of conventional sealing systems. These seals utilize a metallic or elastomeric bellows arrangement,
replacing traditional secondary seals such as O-rings. This unique design eradicates common problems associated with shaft seals, including wear and tear, and ensures optimum sealing even in extreme temperature variations or corrosive environments.
A key advantage of bellows mechanical seals is their versatility. The design eliminates the need for secondary dynamic seals, making it ideal for handling aggressive chemicals and high-temperature applications. The absence of moving parts in the secondary seal area contributes to an extended lifespan, reducing maintenance costs and downtime which are critical concerns in industrial operations.
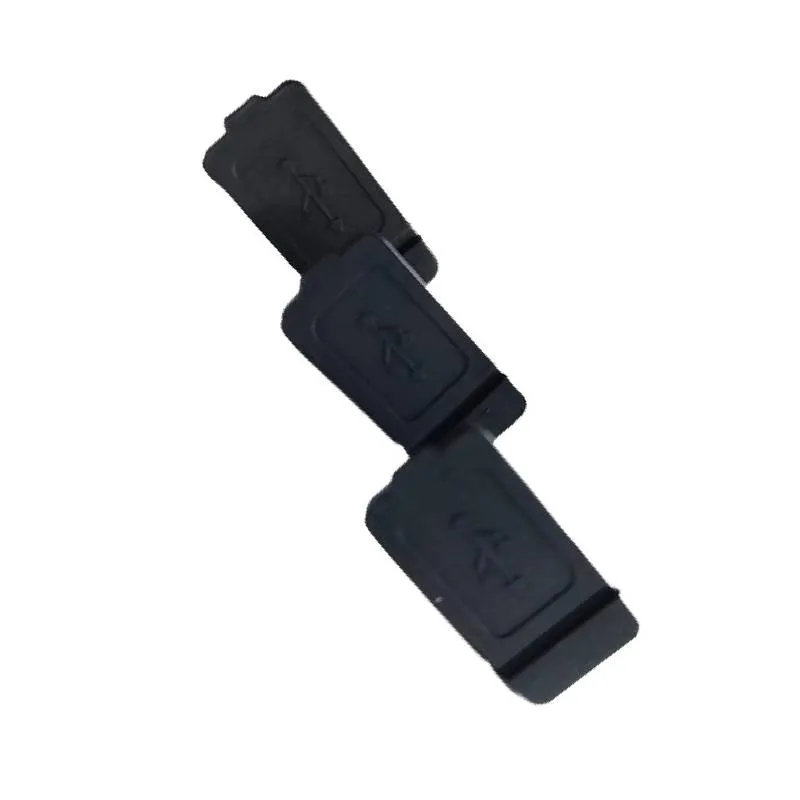
The expertise behind designing bellows mechanical seals involves an intricate understanding of material science and engineering principles. Engineers must select materials that can withstand the process fluids and environmental conditions they will encounter. Metals like stainless steel or high-nickel alloys are often preferred for their exceptional corrosion resistance. In specific applications, elastomeric bellows made of materials like PTFE are employed, offering superior chemical compatibility and flexibility.
Authoritative insights into bellows mechanical seal manufacturing reveal a commitment to precision engineering. Each seal is subject to rigorous quality control measures, ensuring that they meet stringent industry standards. Advanced computational tools and testing facilities aid in simulating operating conditions, identifying potential failure points, and optimizing designs accordingly. The reliance on technological innovations underscores their reliability in critical operations where failure is not an option.
bellows mechanical seal
Trustworthiness in the context of bellows mechanical seals is bolstered by their track record of performance in highly demanding environments. Users often report improved efficiency in their systems, attributed to the seal’s capability to maintain a consistent barrier between different fluid environments under dynamic conditions. Additionally, manufacturers typically offer detailed documentation and certifications, assuring compliance with international safety and quality standards.
Real-world experiences provide valuable insights into the practical applications of bellows mechanical seals. A case study in the petrochemical industry highlighted the seal's ability to withstand high-pressure applications without degradation over time, leading to significant cost savings and enhanced operational safety. Another instance in the pharmaceutical sector demonstrated how the aseptic design of bellows mechanical seals prevented contamination, contributing to better product purity and process integrity.
For companies looking to optimize their operational efficiency and reduce cost implications associated with leakage and maintenance, bellows mechanical seals present an advantageous solution. Consultation with experts ensures that the correct seal type is selected based on specific application requirements, further reinforcing their role in enhancing process reliability.
As industry demands continue to evolve, so too does the innovation behind bellows mechanical seals. Continued research and development are fostering advancements in materials and seal design, increasing their applicability across emerging markets and technologies. Their contribution to achieving sustainable practices cannot be understated, as they help minimize wastage and improve energy efficiency across systems.
In conclusion, bellows mechanical seals are testament to the marriage of engineering excellence and industrial necessity. Their critical role in sustaining operational integrity across diverse applications showcases their indispensability. Through continuous innovation and adherence to quality, they not only meet but often exceed industry expectations, making them a cornerstone in modern mechanical sealing solutions.