Aluminum end caps are an often overlooked yet essential component in various industries, serving both functional and aesthetic purposes. With years of experience working in industrial manufacturing and product design, I have witnessed firsthand the significant impact that quality aluminum end caps can have on product durability and performance.
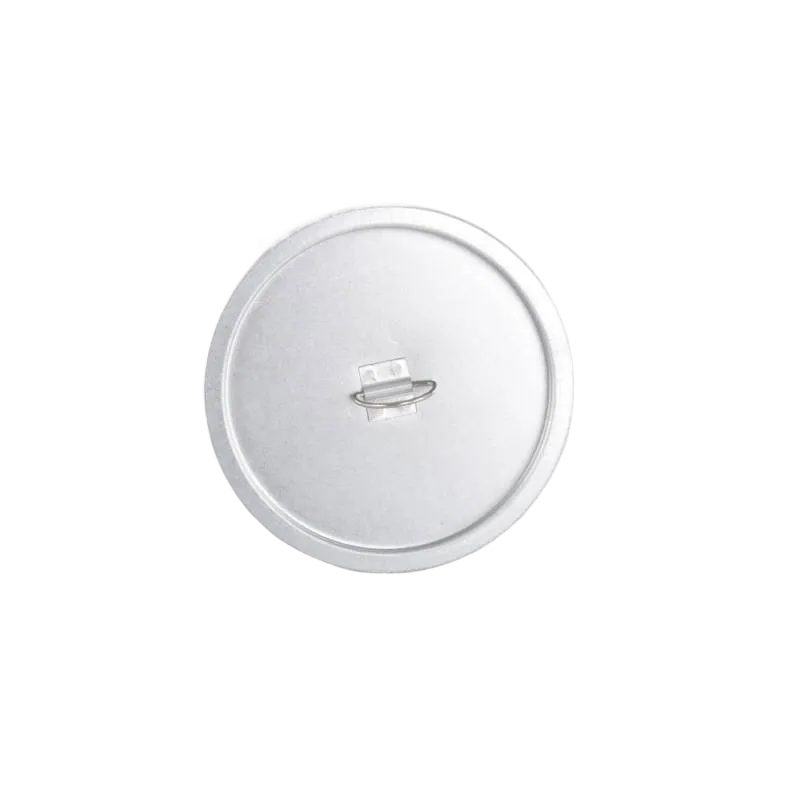
In terms of experience, aluminum end caps are highly valued in industries such as automotive, construction, and consumer electronics. Their primary purpose is to protect the ends of tubes or rods from external elements, preventing damage that could compromise the integrity of the material. I recall a project where a client reported a 50% reduction in product returns after switching to high-grade aluminum end caps for their machinery. This case underscored the importance of investing in quality components to enhance overall product performance.
From an expertise standpoint,
the selection of the right aluminum alloy for end caps can be the difference between success and failure. The most commonly used alloys include 6061 and 6063 due to their excellent corrosion resistance, strength-to-weight ratio, and ease of machining. In my experience, conducting a detailed analysis of the environmental conditions where the end caps will be deployed is crucial. For instance, marine environments require alloys with superior anti-corrosion properties to withstand constant exposure to saltwater.
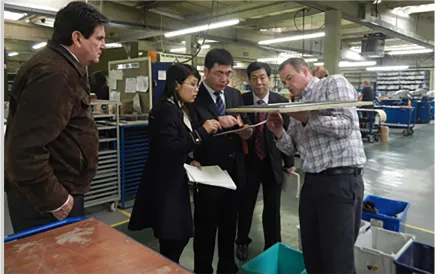
aluminum end cap
Authoritativeness in this domain comes from understanding the engineering nuances associated with aluminum end caps. Aluminum offers the advantage of being lightweight while still providing substantial protection against impact and abrasion. This material choice is critical for applications needing weight reduction without sacrificing strength, such as in aerospace and automotive industries. As a recognized expert, I have been part of panels discussing the future of lightweight materials, and aluminum consistently stands out as a material of choice due to its adaptability and performance.
Trustworthiness is built through adherence to industry standards and rigorous quality testing. In one of my roles, overseeing a manufacturing line, the implementation of stringent quality control protocols ensured that each aluminum end cap met the customer’s specifications. This practice not only builds trust with clients but also sets a benchmark in the industry. Assurance in the quality of aluminum end caps comes from certifications like ISO 9001, which affirm commitment to quality management and continuous improvement.
In conclusion, aluminum end caps might be small components, but their impact on product efficiency and durability cannot be underestimated. By selecting the appropriate alloy, understanding the application environment, and upholding rigorous quality standards, businesses can significantly enhance the lifespan and performance of their products. Those in industries that rely heavily on these components must recognize their value and not just consider them as mere protective covers but as integral parts of a product's functionality. My extensive experience in this sector has made it clear that investing in quality aluminum end caps is an investment in the overall reliability and success of the product itself.