Alloy washers may seem like a modest component in the grand scheme of mechanical design, but these small metallic rings hold pivotal roles in various industrial applications. In a world where precision engineering dictates success, the importance of alloy washers cannot be overstated. This article delves into their intricate features, uses, and benefits, backed by professional insights and a wealth of experience in the field.
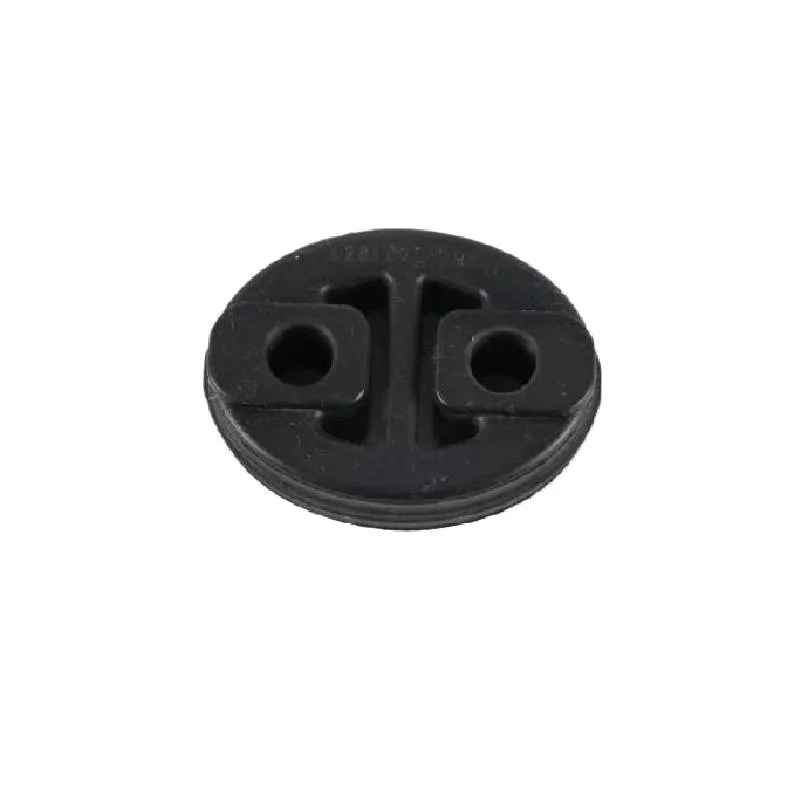
Engineered for durability, alloy washers are crafted from a blend of metals, each contributing to enhanced performance traits that surpass traditional washers. The choice of alloy—whether it be aluminum, brass, copper, or stainless steel—is determined by the washer's intended environment and load-bearing requirements. For instance, stainless steel alloy washers are highly resistant to corrosion, making them an optimal choice for marine applications. Meanwhile, copper alloy washers offer exceptional thermal conductivity, suited for heat exchange systems.
In my years of engineering consultancy, selecting the appropriate alloy washer has often been the key to circumventing project failures. Not only do these washers provide even load distribution, but they also mitigate risks of galvanic corrosion in multi-metal assemblies. An improperly chosen washer can lead to equipment malfunction, increased maintenance costs, and even complete system breakdown.
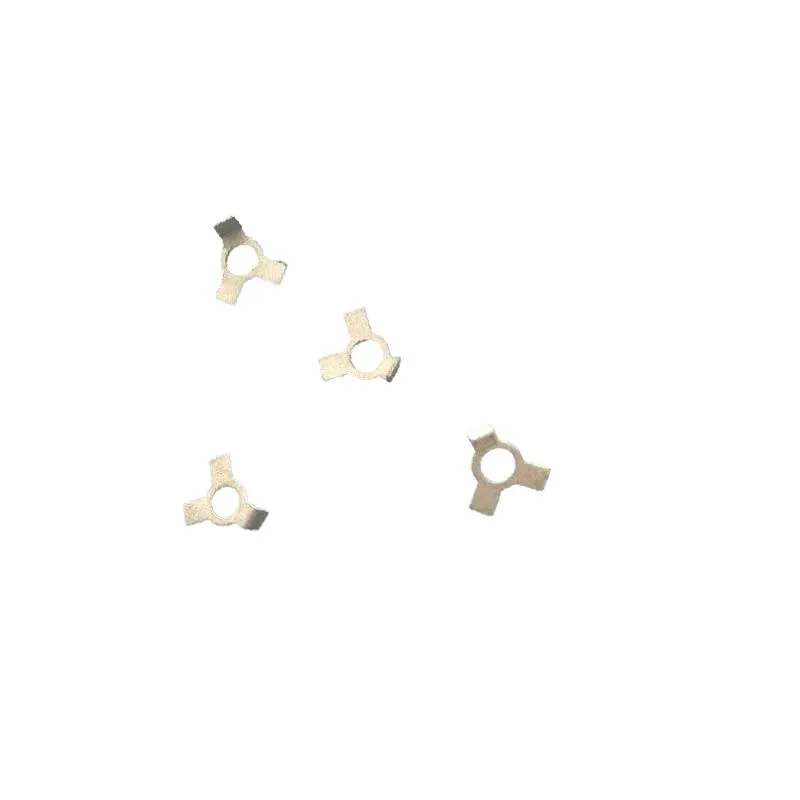
Professionals and engineers alike favor alloy washers for their exceptional reliability under pressure. Compared to non-alloy variants, they exhibit superior tensile strength, which is crucial for machinery exposed to fluctuating loads or vibrations. When devising power transmission systems, for example, failure to account for such dynamics can drastically reduce machinery lifespan.
Alloy washers act as robust buffers, extending the operational longevity by effectively managing stress distributions.
alloy washers
The authoritative consensus in the engineering community is that investing in high-quality alloy washers significantly enhances overall system resilience. Their contribution to operational efficiency is evidenced by minimized downtime and reduced need for frequent replacements. When advising clients, the enduring wisdom is that these initial investments yield high returns through prolonged service life and lower total ownership costs.
Trustworthiness in manufacturing extends beyond the composition and performance of alloy washers to their compliance with international standards. Industry benchmarks such as ISO and ASTM certify that washers meet stringent specifications for dimensional accuracy and mechanical properties. Manufacturers who comply with these standards provide end-users with the assurance of consistent, high-quality components.
Real-world experiences also highlight the necessity of choosing reputable suppliers who not only adhere to standards but also offer customization options. Tailoring washers to specific requirements—be it size, thickness, or alloy composition—can greatly enhance the application’s efficacy. Engineers should insist on detailed project consultations with suppliers to explore these customized solutions.
In conclusion, alloy washers are indispensable in achieving optimal performance and reliability in diverse industrial applications. Their design, rooted in professional expertise and authoritative standards, guarantees their capability to withstand extreme conditions. Trust in their quality and manufacturer adherence to standards ensures that projects not only meet objectives but surpass durability expectations. Through careful selection and expert application advice, alloy washers can significantly contribute to advancing technological innovations worldwide.