The 8-inch steel pipe cap is a vital component in numerous industrial and construction projects, offering both functionality and reliability. Understanding its applications, benefits, and purchasing considerations is crucial for any project that demands high-quality materials and dependable sealing solutions.
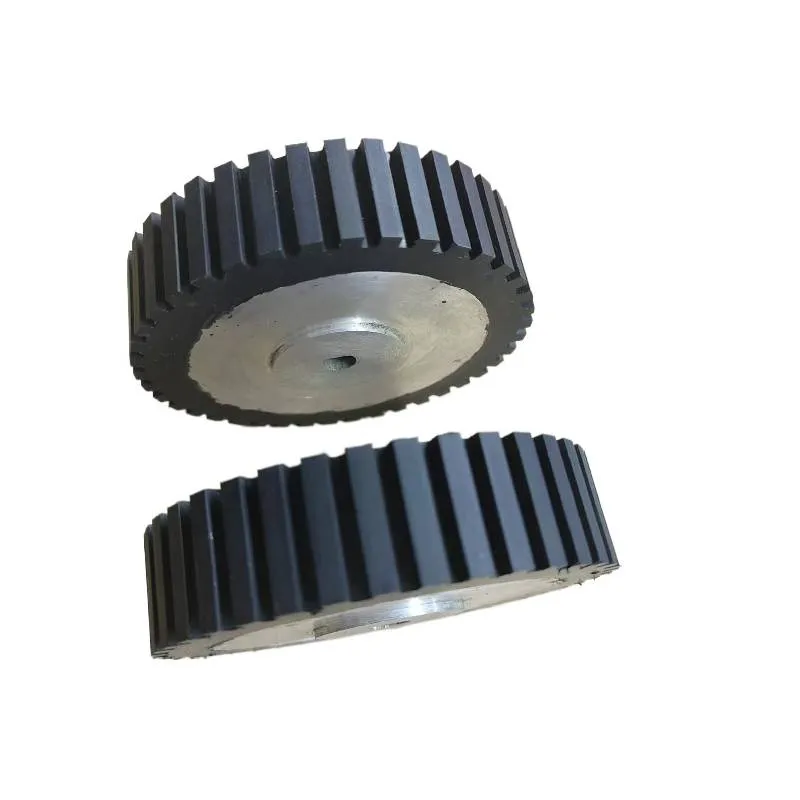
Understanding 8-Inch Steel Pipe Caps
Steel pipe caps are designed to protect the ends of pipes, preventing damage and ensuring a secure seal. The 8-inch variant is particularly sought after in oil and gas industries and plumbing networks that require robust and durable piping solutions. These caps are engineered to fit seamlessly over the pipe ends, shielding them from debris, moisture, and other environmental factors that might compromise their structural integrity.
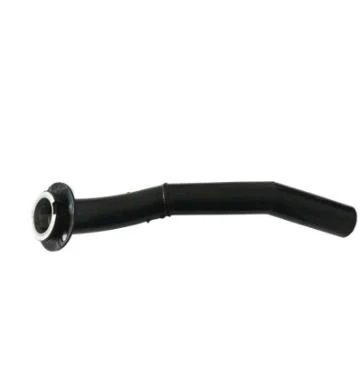
Material and Design
The standard material for these caps is carbon steel. This choice is due to its exemplary tensile strength, resistance to temperature fluctuations, and long-term durability. The design often features a welded seam or a threaded fitting, depending on the application's specific demands. Welded caps provide a permanently secure cover, ideal for infrastructure that doesn't require frequent maintenance or disassembly. In contrast, threaded caps offer flexibility for systems that need periodic inspection or expansion.
Applications and Benefits
The versatility of the 8-inch steel pipe cap extends across various industries
1. Oil and Gas Exploration These caps are essential for capping off exploratory wells and ensuring that no contaminants enter the system during downtime.
2. Water Treatment In facilities where large-diameter pipes are common, these caps help in temperature regulation and maintenance by sealing off unused pipe sections.
3. Construction They are indispensable in large infrastructure projects where pipes need temporary closure to prevent debris intrusion.
8 inch steel pipe cap
4. Chemical Processing Steel pipe caps ensure that chemicals are contained within pipes, safeguarding against accidental leaks and environmental contamination.
Expert Installation Advice
Installation of a steel pipe cap, though seemingly straightforward, demands meticulous attention to detail. A critical step involves cleaning the pipe end to eliminate any debris or excess moisture. Position the cap securely, ensuring that there are no gaps between the cap and the pipe edge. For weld-on applications, expertise in welding is vital to prevent surface imperfections that could compromise the seal. Threaded caps should be torqued to the manufacturer’s specifications to prevent leaks without damaging the threading.
Expertise in Selection
Selecting the right pipe cap involves considering the working pressure and temperature conditions of the intended environment. Experts advise opting for caps that exceed the system’s maximum operational pressure to enhance safety margins. Additionally, evaluating the pipe system's overall chemistry is vital to avoid galvanic corrosion, which could lead to premature failure.
Quality Assurance and Trust
When sourcing steel pipe caps, working with reputable manufacturers is indispensable. Quality assurance certifications such as ISO standards provide an added layer of confidence. These assurances verify that the materials and manufacturing processes meet rigorous quality and safety benchmarks. By partnering with trusted suppliers, projects can mitigate risks, reduce costs associated with component failures, and uphold regulatory compliance.
Conclusion
The 8-inch steel pipe cap is an indispensable element in many industrial settings, providing essential protection and sealing for piping systems. By emphasizing careful selection, expert installation, and reliable supplier partnerships, you can ensure that these components not only meet but exceed project expectations. Whether the focus is on longevity, safety, or operational efficiency, the right steel pipe caps are a prudent investment in the successful execution of any large-scale infrastructural endeavor.