The 6-inch steel pipe cap, essential in various industries, has gained popularity due to its functionality and robustness. These caps serve critical roles in ensuring the integrity and safety of piping systems, whether in oil and gas, chemical processing, or construction. Selecting the right steel pipe cap involves understanding its applications, construction, and standards, further emphasising the need for expertise in the field.
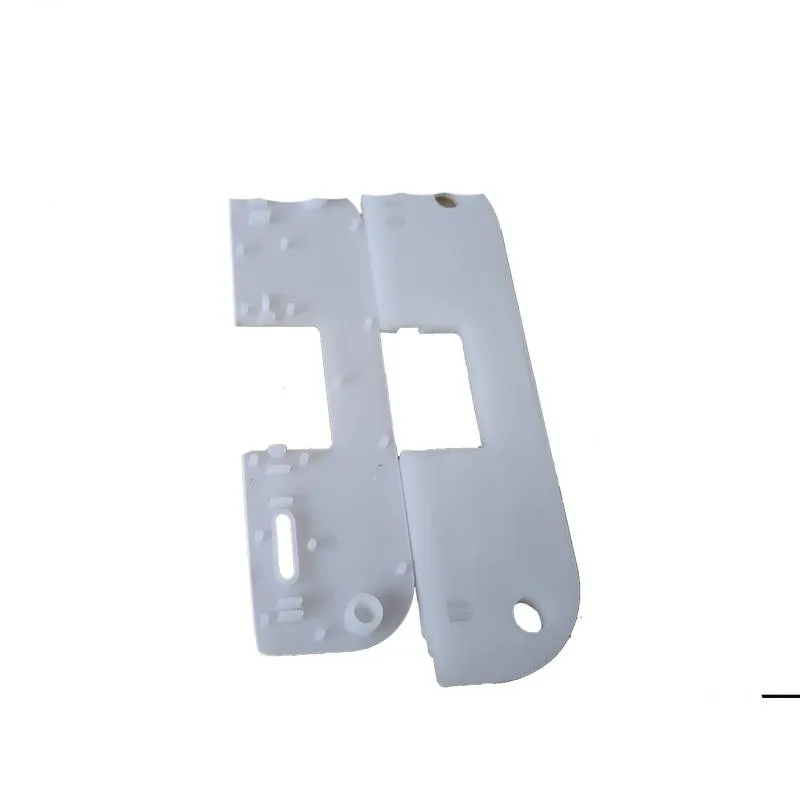
Steel pipe caps are primarily designed to protect pipe ends and prevent any unwanted substances from entering the pipe system. This function is vital in maintaining the system's efficiency and extending the life of the machinery by preventing external contaminants and maintaining necessary pressure within the pipes. Their impressive durability stems from high-grade material used in manufacturing, such as carbon steel or stainless steel, which offers excellent resistance to corrosion and extreme temperatures.
From an expert's perspective, the use of 6-inch steel pipe caps involves meticulous understanding of pressure ratings and compatibility with existing pipe systems. Careful selection is based on ANSI or ASME standards, which cover the manufacturing specifications, dimensions, and wall thickness requirements. Adhering to these standards ensures that the caps are suitable for operations they are intended for, minimizing the risk of failures that could lead to costly downtimes or hazardous leaks.
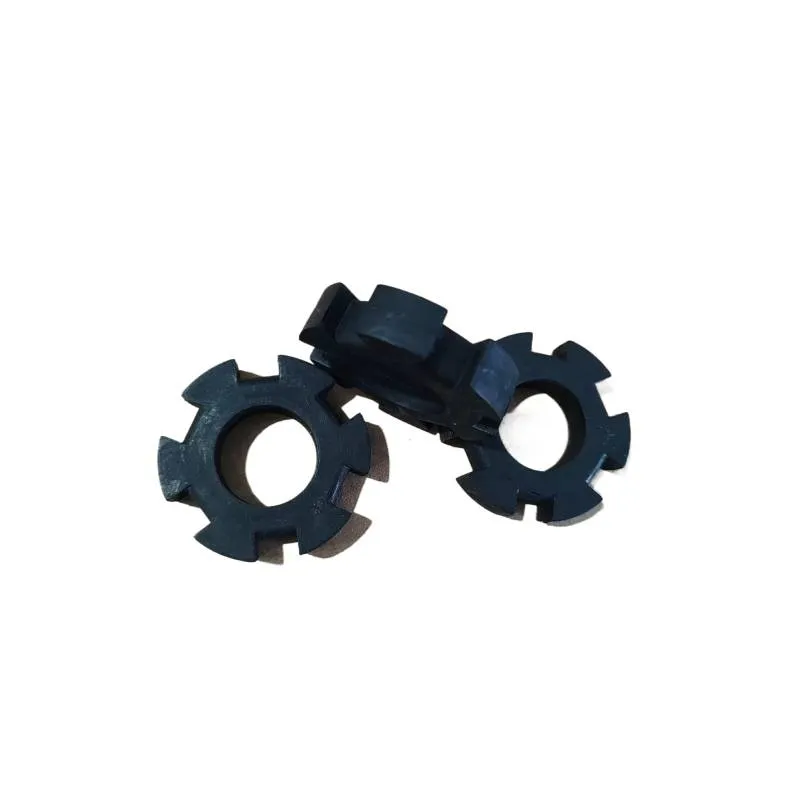
Moreover, these caps are available in a range of designs, including threaded caps and weld-on versions. Threaded caps offer simplicity and quick installation, ideal for situations where frequent maintenance or inspection is necessary. In contrast, weld-on caps provide a permanent solution, sealing the pipe completely for applications where reassessment or pipe modifications are infrequent. An authoritative understanding of these options allows a professional to recommend the most effective type for specific industrial needs.
6 inch steel pipe cap
Trust is paramount when testing the reliability of pipe caps. Manufacturers who adhere strictly to industry standards gain reputability for their products' safety and effectiveness. Through quality assurance processes, such as X-ray inspections or hydrostatic tests, these components undergo rigorous checks to handle anticipated operating pressures adequately. The expert evaluation of a manufacturer’s track record for quality and compliance with safety certifications, like ISO 9001, ensures that consumers receive reliable products.
Sharing experiences from the field reveals the necessity of customizing steel pipe caps to fit unique project specifications. This customization might include altering dimensions or incorporating additional protective layers for chemical resistance. Such transformations necessitate a collaborative effort between engineers and manufacturers, ensuring that parameters like thickness, material grade, and fitting type align perfectly with the customer’s requirements.
Challenges, such as navigating fluctuating costs of raw materials that affect pricing or sourcing caps that offer extreme durability for specialized conditions, highlight the importance of engaging with knowledgeable suppliers. Experience teaches that effective supply chain management and long-term partnerships with trusted manufacturers mitigate such obstacles.
Conclusively, the 6-inch steel pipe cap not only serves as a pivotal component in industrial settings but also exemplifies the synchronization of design, standards, and operational efficiency. Professionals will continually prioritize expert advice and trusted partnerships to leverage innovations in pipe cap manufacturing. By doing so, they uphold safety and performance standards, ensuring resilience and reliability in complex systems, an ethic underscored by their profound impact on industry-wide practices and developments.