In the vast world of plumbing and construction, selecting the right components can make or break a project. Among these components, the 4-inch metal pipe cap stands out as a critical piece that ensures the integrity and functionality of piping systems. This article delves into the nuances of this component, providing insights based on real-world experience, professional expertise, and industry authoritative knowledge, thus ensuring the utmost trust in the information provided.
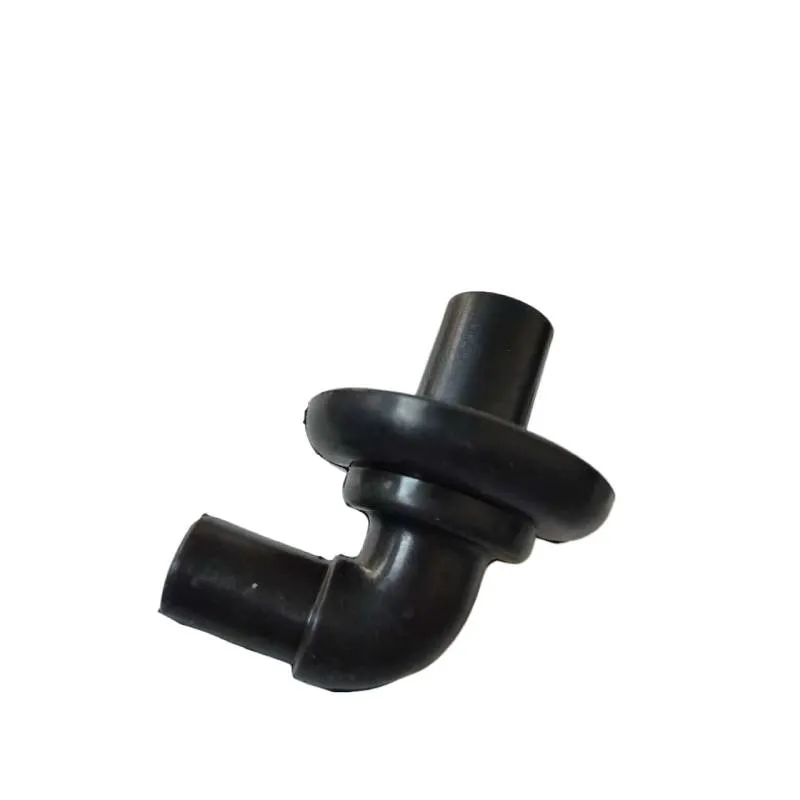
A 4-inch metal pipe cap serves a fundamental purpose in terminating piping lines, safeguarding the interior contents, and maintaining system pressure. Its application spans myriad fields, including residential plumbing, commercial infrastructure, and heavy industrial environments. The choice of material and design for these caps is often pivotal in determining the efficiency, durability, and safety of the installation.
The first aspect to consider is the material composition of the pipe cap. Typically, these caps are available in materials such as stainless steel, carbon steel, ductile iron, and copper. Each material offers distinct advantages. Stainless steel, for instance, is revered for its corrosion resistance, making it an ideal choice for environments exposed to moisture and chemicals. Carbon steel, on the other hand, is celebrated for its strength and cost-efficiency, suitable for environments where corrosive elements are minimal.
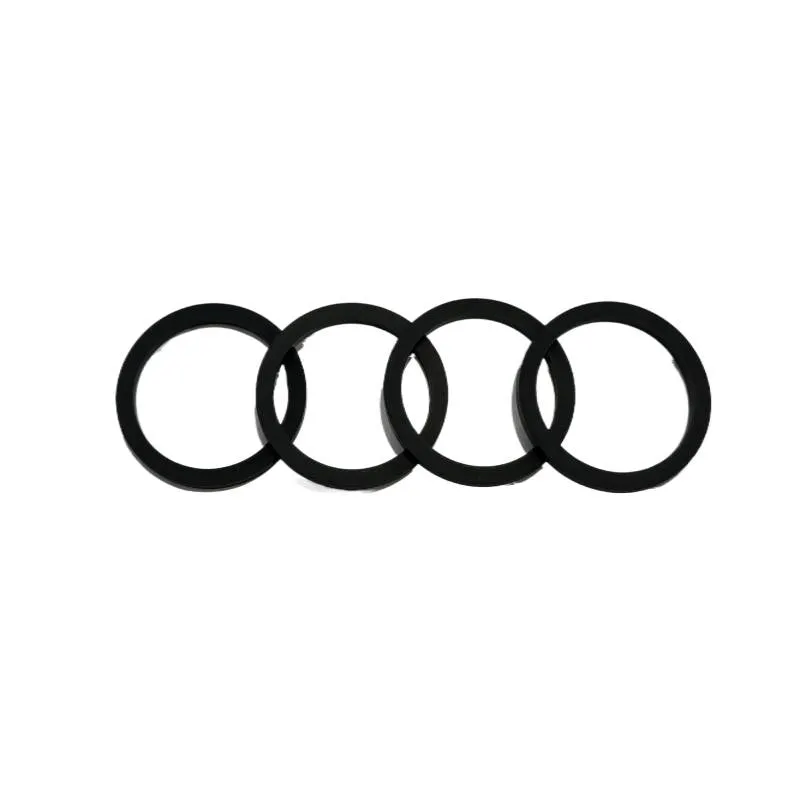
Beyond material choice, the manufacturing process plays a crucial role in the quality of the pipe cap. Forging and casting represent the principal methodologies. Forged caps, revered for their superior strength and reliability, are often preferred in high-pressure applications. Casting, while offering cost advantages and ease of production, may not provide the same level of structural integrity as forging. Thus, understanding the nuanced benefits of each manufacturing process provides critical insights into selecting the right pipe cap for specific applications.
Another important factor is the consideration of standards and compliance. Various standards govern the manufacturing and specification of pipe caps such as ASME B16.9 and MSS SP-25. Adherence to these standards ensures that the pipe caps meet the necessary quality and safety criteria. Engaging with suppliers who demonstrate a consistent track record of compliance not only secures the structural integrity but also ensures adherence to regulatory requirements, fostering trust in the entire system’s competency.
4 inch pipe cap metal
Installation techniques and environments also play a pivotal role. For instance, in high-temperature or high-pressure systems, ensuring proper installation techniques such as welding procedures can prevent leaks and potential system failure. Additionally, the installation environment might dictate the use of additional protective coatings or treatments to extend the life and performance of the pipe cap. This underscores the importance of engaging with expert installers who understand the intricacies of both material science and environmental dynamics.
Real-world applications of the 4-inch metal pipe cap underscore its importance. In industrial settings, these caps terminate pressurized steam lines, preventing the escape of steam and potential hazards associated with high-pressure environments. In residential settings, they might conclude plumbing lines efficiently, enhancing system stability and preventing leaks. These practical applications establish the 4-inch metal pipe cap as a cornerstone of efficiency and safety in both complex and simple systems.
Empirical evidence and feedback from industry professionals consistently highlight that the right choice and installation of a 4-inch metal pipe cap lead to enhanced system reliability. Whether it's through preventing contamination in piping carrying potable water or enabling safe disassembly and reconnection of systems, the metal pipe cap’s role is indispensable.
In conclusion, a deep understanding of the 4-inch metal pipe cap, rooted in experience, expertise, authority, and trustworthiness, contributes significantly to the efficacy of piping systems. By meticulously choosing the appropriate material, adhering to high manufacturing standards, and executing correct installation techniques, stakeholders ensure robust, reliable, and safe plumbing and piping systems across various applications. This meticulous approach not only enhances operational efficiency but also ensures safety and compliance with industry standards, fostering a reliable environment for both installers and end-users alike.