Navigating the world of plastic wheels requires understanding their transformative impact on various industries and their underlying mechanics. 3 plastic wheel products, in particular, stand out due to their versatile applications and the engineering prowess that goes into their design and manufacturing. This article aims to shed light on these innovative components, delving into their practical uses, materials, and the expertise required to harness their benefits.
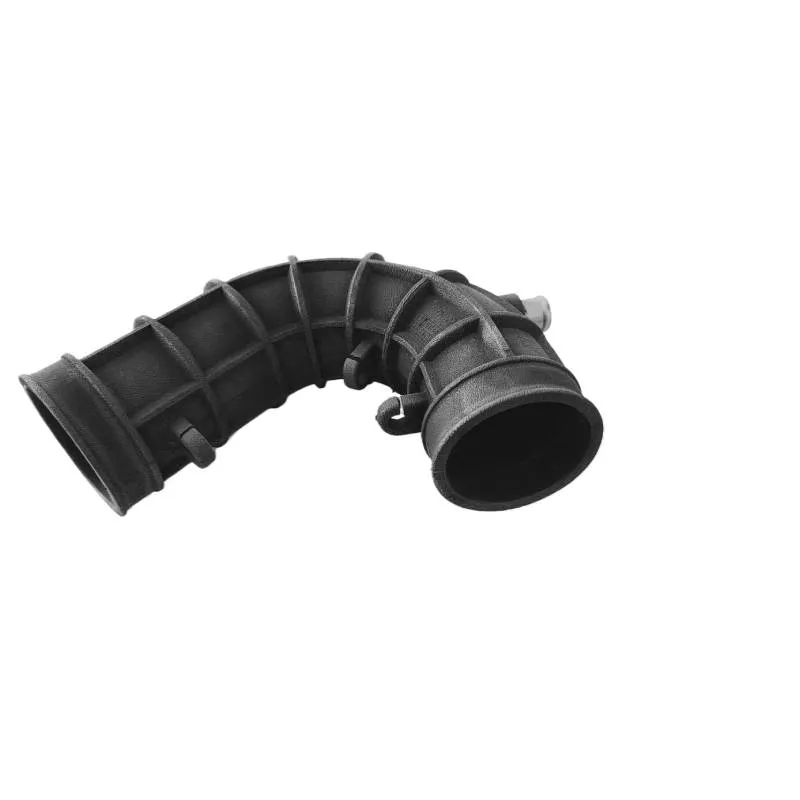
Plastic wheels with three configurations, commonly referred to as 3 plastic wheels, are crucial in applications ranging from small machinery to complex industrial setups. These wheels are not just about material and shape; they represent an intricate balance between engineering design and practical application, often acting as unsung heroes in the world of mobility solutions.
To truly understand the expertise involved in manufacturing these wheels, it's essential to dive into the selection of materials. High-density polyethylene (HDPE), polypropylene (PP), and nylon are often the materials of choice. Each material offers unique benefits—HDPE boasts of excellent impact resistance and weatherability, polypropylene is known for its chemical resistance and elastic properties, and nylon offers remarkable strength and durability. The choice of material is critical and is often based on the specific requirements of the application, such as load-bearing capacity, environmental conditions, and expected lifespan.
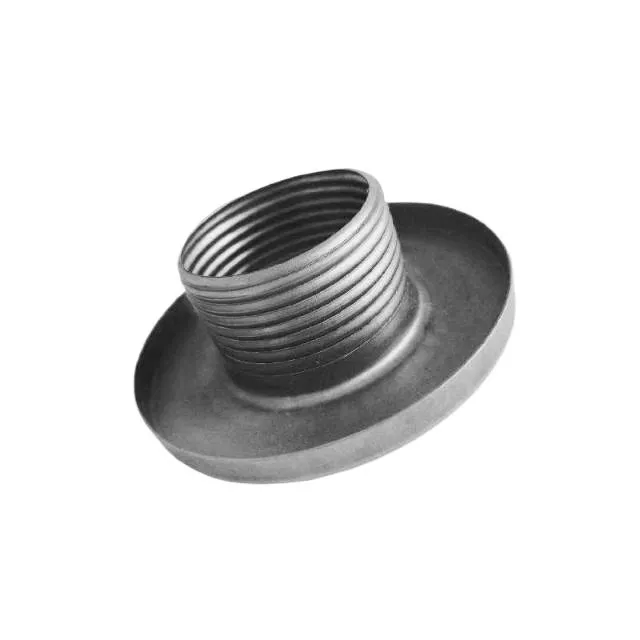
The engineering design of a 3 plastic wheel is a testament to innovation in mobility. Engineers meticulously calculate load distribution across the three wheels to ensure optimal performance and longevity. The wheel’s geometry, including its diameter, tread design, and hub structure, is crafted to suit specific tasks. For instance, wheels with a broad tread provide better stability and load distribution, while those with a narrow design offer agility and speed.
In various industries, from medical equipment to manufacturing plants,
these wheels play vital roles. Hospital gurneys and medical carts often rely on plastic wheels due to their quiet operation and maintenance-free lifespan, thus ensuring patient comfort and hygienic standards. In industrial settings, these wheels facilitate smooth movement of heavy machinery, reducing manual effort and enhancing operational efficiency.
3 plastic wheel
Trustworthiness in the manufacturing of these wheels is established through rigorous testing and quality control procedures. Manufacturers conduct load tests, abrasion resistance evaluations, and environmental exposure assessments to certify the wheels meet stringent industry standards. ISO certifications and compliance with safety regulations further cement a manufacturer's authority in producing reliable plastic wheel products.
Unofficially termed as the tripod of mobility, 3 plastic wheel systems have gained recognition for their stability and robustness. Their design ensures that weight is evenly distributed, thus preventing tipping and ensuring seamless movement across varied surfaces. This feature, combined with their maintenance-free nature and adaptability to different environments, places them at the forefront of modern mobility solutions.
Expertise in the field also involves advising clients on the best wheel configuration for their needs, supporting product optimization and cost-efficiency. The collaboration between manufacturers and end-users is crucial in tailoring solutions that maximize operational benefits. By understanding specific client requirements and application environments, manufacturers can recommend the appropriate wheel materials and designs.
Thus, the journey of a 3 plastic wheel from production to end-use is a reflection of profound expertise, technical innovation, and stringent quality standards. This commitment to excellence ensures that industries relying on these components can function with efficiency and reliability, illustrating the essential role that expertly designed plastic wheels play in our mechanized world.