Navigating the intricate world of 16 plastic wheels may seem trivial to some, but for industry professionals and enthusiasts, it's a landscape rich with opportunity and innovation. As experts in material science and manufacturing processes, we delve into the myriad applications and characteristics of these wheels that set them apart in a competitive market, further fostering their reputation for durability, efficiency, and versatility.
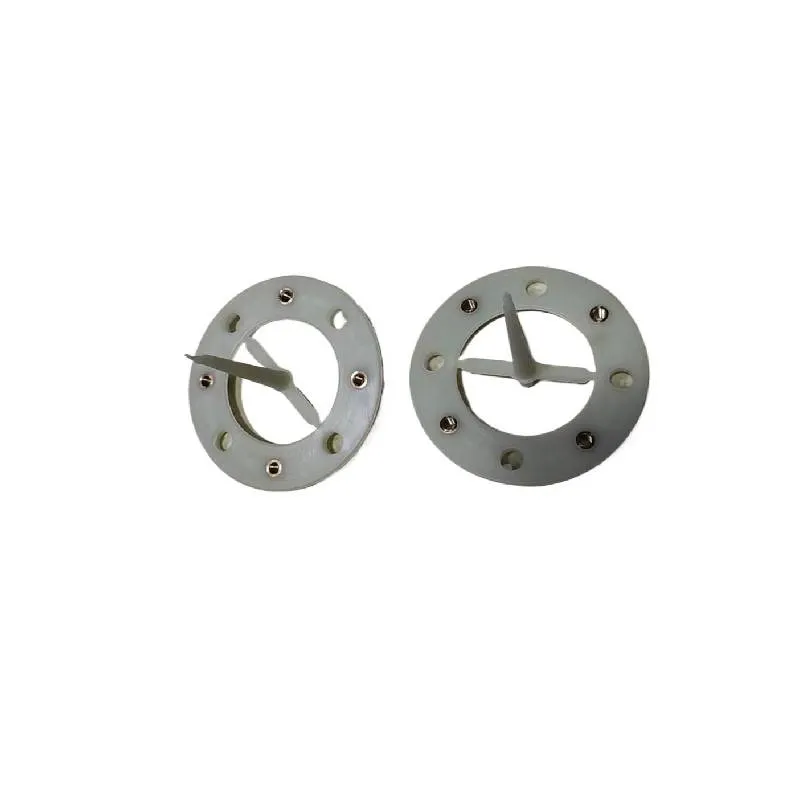
In the realm of manufacturing and industrial applications, 16 plastic wheels are not merely components but pivotal players that enhance both efficiency and usability. These wheels are prized for their lightweight nature, contributing to reduced shipping costs and easier handling during assembly and maintenance. Their corrosion-resistant properties make them an ideal choice for environments prone to exposure to chemicals or moisture, outweighing traditional materials that may falter over time.
The life span of plastic wheels is largely determined by the quality of materials used in their production. Advancements in polymer technology have led to the development of high-performance plastics that offer superior strength and resilience—paralleling, and in some cases, surpassing metal counterparts. This includes the integration of additives that improve wear resistance, UV stability, and load-bearing capabilities, making these wheels suitable for a broader spectrum of applications.
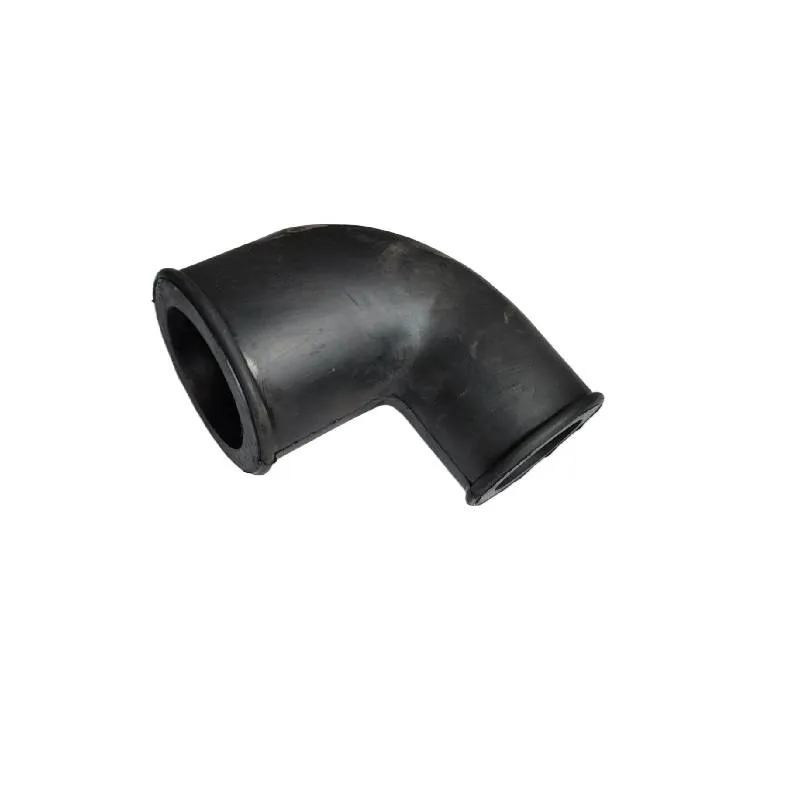
Expertise in the design of 16 plastic wheels also involves a consideration of the engineering principles that govern their function. The structural design, including tread patterns and interior ribbing, is as crucial as the material composition. Engineers utilize computer-aided design (CAD) software to simulate stress tests before production, ensuring that each wheel meets stringent industry standards. These simulation results guide the refinement of the wheel's design, maximizing performance under various operational conditions.
16 plastic wheel
The credibility of 16 plastic wheels is further bolstered by compliance with international standards and certifications. Whether employed in automotive assemblies, medical equipment, or consumer goods, these wheels undergo rigorous testing to certify their safety and efficiency. Many manufacturers invest in continuous research and development programs and collaborate with academic institutions to innovate and stay ahead of industry trends, thereby maintaining their authoritative stance in the marketplace.
Trustworthiness in the context of plastic wheels extends beyond product performance and into the sphere of environmental responsibility. Increasingly, manufacturers are adopting eco-friendly practices by utilizing recycled materials and minimizing production waste. This commitment serves to not only enhance consumer trust but also adheres to global sustainability initiatives, thus setting a precedent in corporate responsibility within the industry.
For professionals operating in sectors that utilize these wheels, firsthand experience often reveals insights that traditional data sheets can't convey. Consultations with industry experts and participation in networking events often expose end-users to novel applications or emerging trends, such as smart wheel technologies integrating sensors for predictive maintenance. This evolving interaction between users and manufacturers ensures that the development of plastic wheels remains aligned with real-world demands and technological advancements.
In summary, the segment of 16 plastic wheels illustrates the intricate blend of technology, science, and innovation. From boasting superior material advantages and offering financial savings through weight reduction, to embodying a commitment to sustainability, these products capture the essence of modern industrial evolution. By embracing a continuous exchange of expertise and experience, the industry not only meets the current demands but also prepares for the dynamic challenges of the future.